|
Post by Darksky on Aug 30, 2013 13:06:58 GMT -5
Possible Alternative Titles: Numbers is Hard IIThe Slow Kid Attempts to Retain Most of his Fingers... Starting Point: This is a tree. 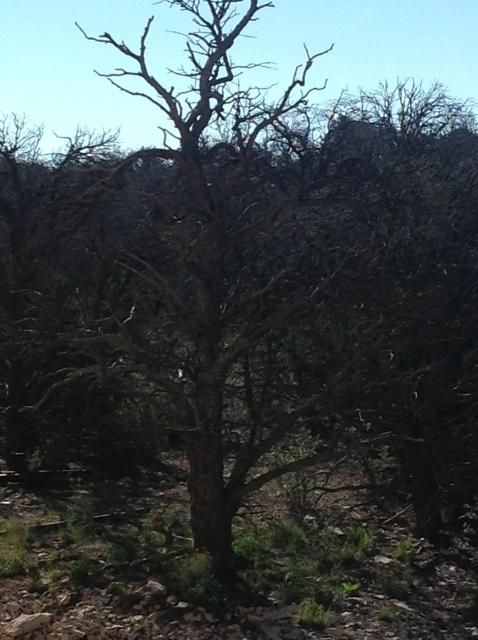
|
|
|
Post by Darksky on Aug 30, 2013 13:10:05 GMT -5
This is also a tree. Smaller, but still a tree. 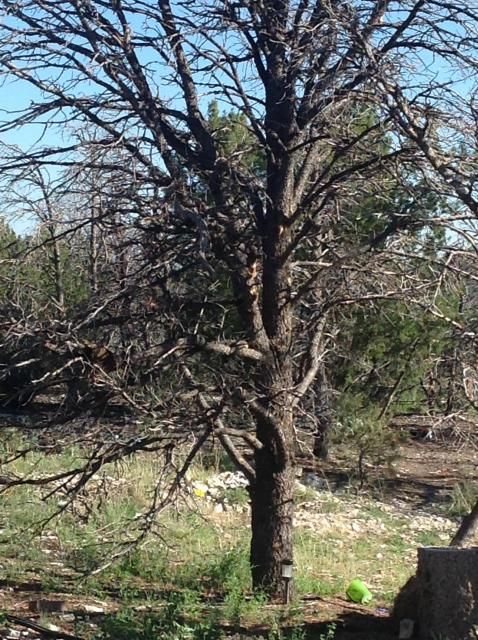
|
|
|
Post by Darksky on Aug 30, 2013 16:00:35 GMT -5
These trees are piñon pine and live in my valley. We are six years into a drought in Southern Colorado. It has resulted in the pine beetle becoming more active. The beetle always exists and lives under the bark of the various pine trees for most of it's life. However during the drought the trees cannot live with the damage caused by the beetles. This results in a large portion of our trees dying off. This phenomenon is referred to as "beetle kill". The trees in the earlier posts are "standing dead".
|
|
|
Post by Darksky on Aug 30, 2013 16:07:59 GMT -5
|
|
|
Post by Darksky on Aug 30, 2013 16:12:17 GMT -5
The first tree, later that day. 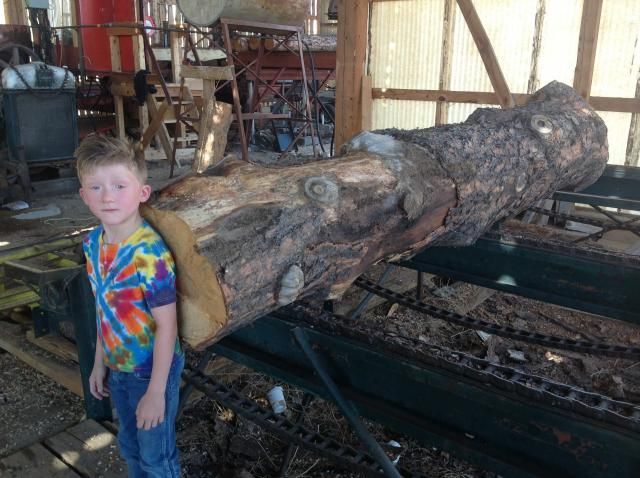
|
|
|
Post by ÈlTwo on Aug 30, 2013 18:41:07 GMT -5
Looking forward to all the steps.
|
|
|
Post by Darksky on Aug 31, 2013 4:11:56 GMT -5
A little less tree like: 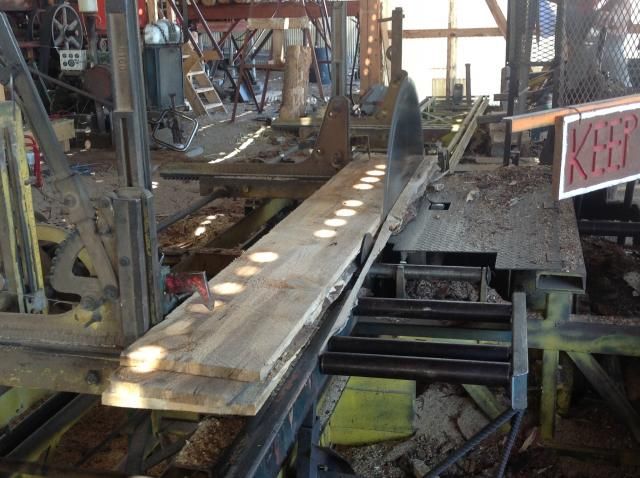
|
|
|
Post by garbulky on Aug 31, 2013 5:28:55 GMT -5
Darksky, your subwoofer project was really something. I can only imagine what your bookshelf speaker would look like.
|
|
|
Post by Topend on Aug 31, 2013 6:35:19 GMT -5
Taking DIY to the next level. I look forward to seeing / reading more.
Dave.
|
|
|
Post by Darksky on Aug 31, 2013 14:01:19 GMT -5
Thanks for the kind words. We shall see if I can meet your expectations.
This project will be a set of LS Encore bookshelf speakers deigned by Danny Richie. He is a really nice guy who seems to be actually invested in the success of people who build with his designs.
This set will be a hybrid, he designed the bookshelves to be small enough to be functional while not sacrificing too much of the performance you would achieve with the minitower version of the same speaker.
I am going to alter his dimensions slightly to accommodate my stock and add a little height to make up for the lost space. This will yield a slightly taller bookshelf that has an internal volume that Isslightly closer to the larger volume of his tower version- this will supposedly yield slightly better low end bass response. I am somewhat dubious of the value of the change, there is a limit. To how much low end you can get from a five inch driver. I will talk more about additional woofer cabinets as the Job progresses.
Bradley
Edit- I apologize for the horrific errors in text. I am using an iPad for my input device. I have crashed my desktop and have not taken the time to reformat as of yet. The auto correct and typing shortcuts that are resident in Apple products are difficult for me to master.
|
|
|
Post by ÈlTwo on Aug 31, 2013 15:51:19 GMT -5
Milling your own lumber is what makes this extra interesting.
|
|
|
Post by Darksky on Aug 31, 2013 17:04:12 GMT -5
I think so. I am hoping that this process furthers my Son's interest in not just audio, but also helps him to grasp the fact that he can design and create anything he sets his mind on.
No matter what else happens, when we are done he will have a set of speakers that he and his father built from scratch. He will literally be able to recall picking the trees that we cut down and took to the mill. I am hoping that these will become a small heirloom that he will have of me.
|
|
|
Post by Darksky on Aug 31, 2013 21:53:43 GMT -5
The first decent look at the lumber: 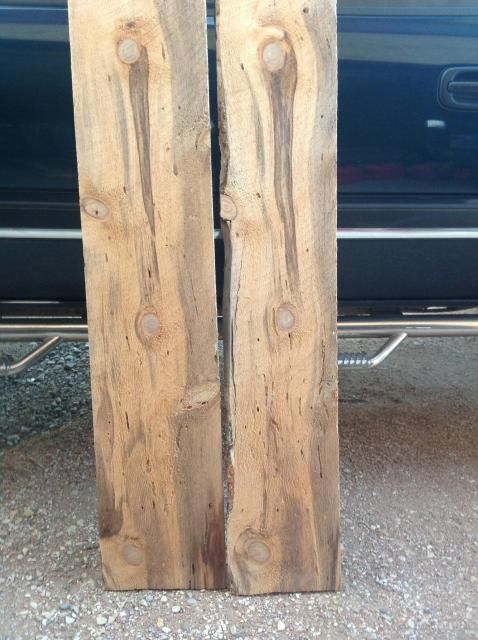 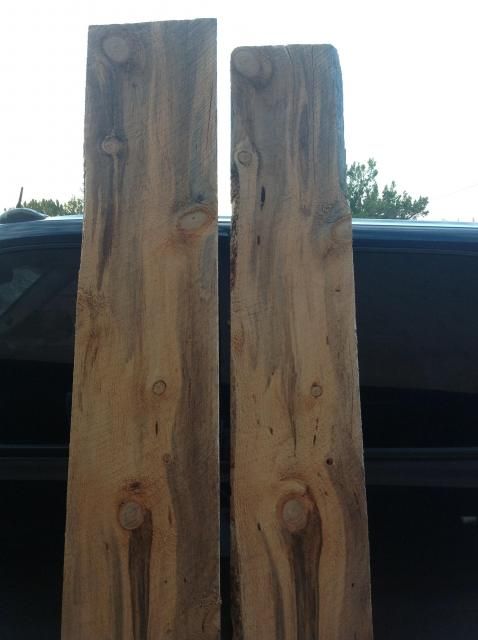
|
|
|
Post by Darksky on Sept 1, 2013 19:09:22 GMT -5
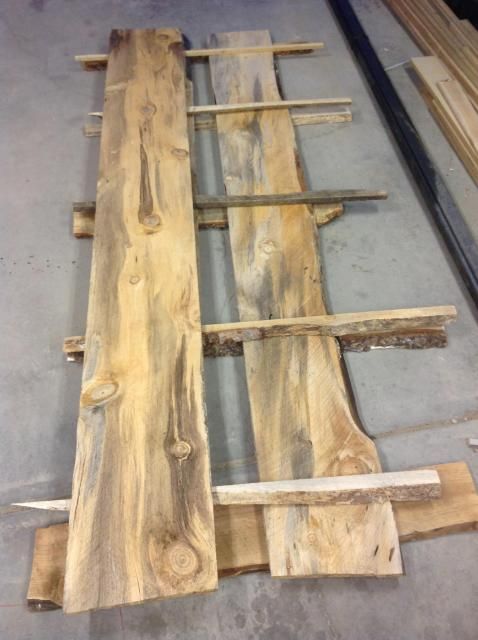 The lumber is currently "stickered" in my shop. I have four beautiful 8 foot long, 1 and 1/8 inch thick by 13 inch wide sticks and two 8 foot long, 1 and 1/8 inch thick by 10 inch wide sticks. Because they were standing dead they are fairly dry. They came off the saw with the wettest one at 14% moisture. Being stickered with air blowing over them is drying them quite quickly. I believe the outer pieces will be ready to work very soon. I have waited to run them through a planer until they dry to my satisfaction, so I may pick the prettiest and straightest pieces before I make them perfectly square. The extra thickness of the 1+ inch aspect will yield good sturdy 1 inch thick finished walls. I have had a few concerns about using a hardwood. (I know that most of the pine family cannot be considered actual hardwood, as they are somewhat soft.) piñon pine is very dense, it has a heavy sappy nature and is very resilient. Friends have voiced concerns over the resonance of using solid wood versus MDF and veneer. I think I can assuage those concerns through a combination of things: 1. The use of true 1 inch thick material adds a significant amount of mass over thinner cabinets. The design of this cabinet is vented as well, so it will not be subject to the same pressures as a sealed box 2. I plan on sealing the inside of the boxes using a spray on rubber sealant. When I built my subwoofers I used *as seen on TV* Flex Seal to seal the joints. It is a remarkably easy to use spray on rubber coating. When wet it is quite adhesive and bonds to MDF or wood extremely well. I have read some and realize now that rubber on the inside of a speaker box can be good or bad depending on the nature of the rubber. Hard rubber (like in a superball) would be bad as it would increase the reflectivity or bounce of the walls. However, soft rubber (butyl) would help to absorb energy. Thankfully, the Flex Seal is very soft, malleable rubber. I believe it will fit the bill perfectly. 3. I have a lining product. No-Rez is a dense foam product with an adhesive backing. It is 1 inch thick and available in sheet form. I have a small sheet that will provide me with enough to line the cabinets completely. It makes me think of the NASA space foam that is being used to make mattresses and mattress pads 4. I will brace the cabinets well with oak material. I even have some 4 inch wide slabs of oak that have been milled down to 1/8 inch thick. I could employ pieces of this material on the flat interior sides of the box to help deaden the walls as needed. 5. The front baffle will be of 3/4 inch MDF with a 1/8 inch piece of plexiglass laminated to it. The drivers will be mounted on the plexiglass face with the screws going through the plexiglass and into the MDF. I have the option of drilling completely through the MDF and using nuts and bolts rather than wood screws. This baffle will snugly fit into dado cut tracks into the walls roof and floor on the inside of the box. Tell me what you think. I am always open to suggestions and criticism. I think this is going to be a fun and educational project for both me and my boy.
|
|
|
Post by gregd on Sept 3, 2013 14:41:14 GMT -5
I have had a few concerns about using a hardwood. (I know that most of the pine family cannot be considered actual hardwood, as they are somewhat soft.) piñon pine is very dense, it has a heavy sappy nature and is very resilient. Friends have voiced concerns over the resonance of using solid wood versus MDF and veneer. I think I can assuage those concerns through a combination of things: The challenge with using solid stock rather than mdf or ply is wood movement. I suppose it would be no problem if you were to run the grain vertically on the baffle, sides, and back provided the top/bottom were essentially end-grain cutting boards. Otherwise I think you'd have a large joint where end grain meets long grain - and that could cause cracking.
|
|
|
Post by Darksky on Sept 3, 2013 15:03:52 GMT -5
Picture of the LS Encore kit: 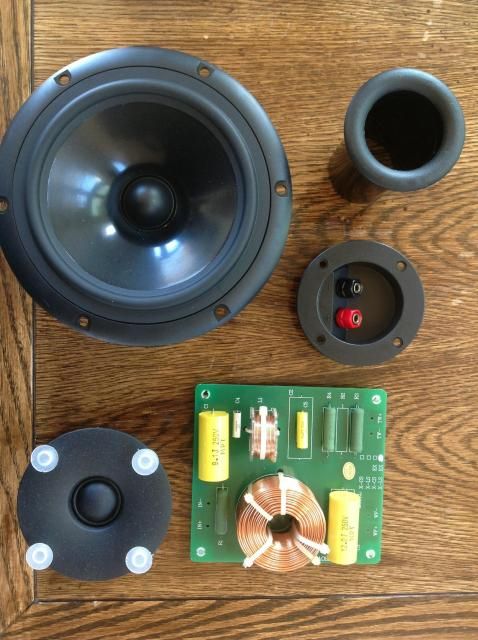 6.5 inch woofer 1 inch tweeter Crossover Port Wiring cup It also came with cardas wire for internal wiring various and sundry screws and connections. I bought one sheet of No-Rez acoustic liner.
|
|
|
Post by solidstate on Sept 3, 2013 16:01:29 GMT -5
uhm
That lumber isn't kiln dried and it will shrink and warp on you.
The best material to use is birch ply or MDF.
There is some great bamboo plywood that would also make good speaker cabinet material.
Bamboo ply is #1 in my books.
|
|
|
Post by Darksky on Sept 3, 2013 16:16:10 GMT -5
Hygrometer reading on test piece is at 11% as of this morning. No checking or warping as of today. Not all lumber is kiln dried. Lots of people have no access to kilns. As I noted before, these trees were standing dead for a full season. I cut four times more stock than I need for this project. I also waxed all the end grain to (tasteless) some of the cracking as it finishes drying. Once it gets down to single digits, I think it will be stable enough to begin.
I have it stickered and under fans. The snickering will keep it flat for the most part. I worry more about the knots opening up where the grain crosses than anything else.
It may turn into "canoe" wood yet, but so far it seems okay.
|
|
|
Post by Darksky on Sept 3, 2013 20:28:27 GMT -5
First drawing: 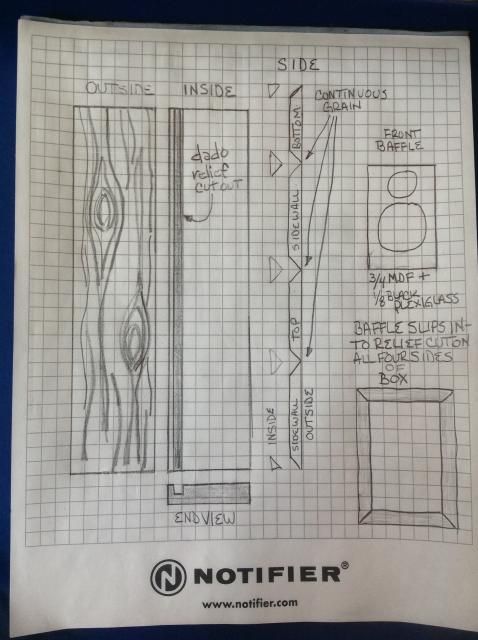 Does this make any sense?
|
|
|
Post by Darksky on Sept 4, 2013 14:05:12 GMT -5
I think the best idea for the rear baffle will be to make an oak lip that sits inside the box 1 inch from the rear of all four walls. Then I can just drop the rear baffle in from the back. Glue it down, maybe put a few headless nails in place to hold it. By setting it in that way, it will not be directly attached to any of the box pieces.
The designer said that increasing the box size from the midline of the woofer down (if that makes sense) will increase the internal volume without negatively impacting imaging.
Keeping this in mind, I am thinking about making them several inches taller, making a false floor in the box that will create a 2 inch high empty space inthe bottom of the box. I can fill this dead space with steel shot. It will add more than ten pounds to each speaker, deaden the box a little more, and concentrate that weight at the very bottom of the box. That will certainly make them more stabile wherever they are placed.
|
|